Foam Moulding: Innovation and Excellence in Polyurethane Foam Solutions
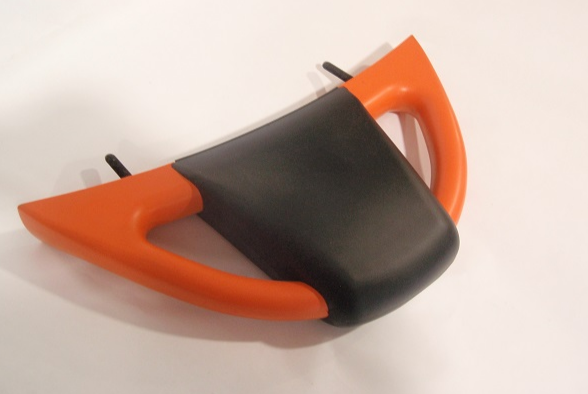
Foam moulding, specifically polyurethane foam moulding, stands out as a cornerstone of advanced manufacturing technologies. Acoustafoam, a leader in this industry with 36 years of experience, has mastered the art of producing high-quality polyurethane moulded foam products. This article delves into the intricacies of foam moulding, emphasizing its applications, benefits, and the specific solutions offered by Acoustafoam.
What is Foam Moulding?
Foam moulding involves shaping foam materials using various techniques to create products that are both functional and aesthetically pleasing. At Acoustafoam, polyurethane foam moulding—also known as Integral Skin or Self Skin moulding—is a specialized process that delivers durable and versatile foam products. This technique combines expert design with advanced manufacturing methods to produce foam items with an integral skin that provides enhanced durability and a high-quality finish.
The Process of Foam Moulding
Raw Material Preparation
The foam moulding process begins with the preparation of polyurethane foam. This material is chosen for its exceptional properties, including its flexibility, durability, and resistance to various environmental factors. The foam is mixed with other components to achieve the desired consistency and characteristics.
Moulding and Curing
Once the foam mixture is ready, it is dispensed into specially designed moulds. During the moulding process, a chemical reaction takes place, causing the foam to expand and fill the mould. This reaction also forms a tough, flexible skin on the exterior of the foam, which is essential for providing protection against scratches, wear, and tear.
The moulds used in this process can be chemically etched to create various textures and finishes, such as leather-like patterns. After moulding, the foam is cured to ensure that it reaches the desired hardness and stability.
Trimming and Finishing
After curing, the foam products are removed from the moulds and undergo a trimming operation to remove any excess material. This step ensures that the final product meets the specified dimensions and quality standards. Additional finishing touches, such as coating with UV stable paint, are applied to enhance the product’s appearance and longevity.
Applications of Foam Moulding
Foam moulding is incredibly versatile, with applications spanning various industries. Here are some notable uses of polyurethane foam moulding:
Automotive Industry
In the automotive sector, foam moulding is used for components such as grab handles, armrests, steering wheels, and headrests. The integral skin provides a comfortable touch and durability, making it ideal for automotive interiors.
Furniture and Home Decor
Foam moulding is also prevalent in the furniture industry. It is used to create cushions, seating, and decorative trims. The flexibility and aesthetic options available with foam moulding make it a popular choice for creating customized furniture pieces.
Marine and Industrial Applications
For marine applications, foam moulding offers solutions such as seating and protective components. In industrial settings, foam moulding is used for insulation and protective barriers, thanks to its resistance to various environmental conditions.
Safety and Gaming Industries
Foam moulding provides solutions for safety products like impact-absorbing pads and gaming accessories. The material’s ability to absorb impact and provide cushioning makes it suitable for these applications.
Benefits of Foam Moulding
Durability and Flexibility
One of the significant benefits of foam moulding is the durability of the final product. The integral skin formed during the moulding process is resistant to abrasion, scratches, and wear. Additionally, the flexibility of polyurethane foam allows it to be shaped into various forms, making it suitable for different applications.
Customization and Design Options
Foam moulding offers extensive customization options. The moulds can be designed to create textures and finishes that meet specific aesthetic and functional requirements. This level of customization is particularly valuable in industries that demand unique product designs.
Protection and Insulation
Foam moulding provides excellent protection against impacts and environmental factors. The foam’s insulating properties make it ideal for applications requiring thermal or acoustic insulation. This is particularly beneficial in automotive and industrial applications where insulation is critical.
Rapid Prototyping and Production
Acoustafoam’s expertise in foam moulding allows for rapid prototyping and quick turnaround times. This capability is crucial for industries that require fast development and testing of new products. The ability to produce prototypes quickly helps in refining designs and speeding up the product development process.
Read Also: Understanding the Legal Implications of Health Sharing Plans for Small Businesses
Key Products and Solutions
Acoustafoam offers a range of foam moulding products and solutions tailored to various industry needs. Some of their key products include:
Integral Skin Mouldings
These are available in various hardness levels, ranging from 25 to 90 Shore A. They can be produced using resin, aluminium, or steel tooling, and are suitable for low, medium, and high-volume production. Integral skin mouldings are used in automotive components, furniture, and more.
Acoustic Barrier Products
Acoustafoam’s acoustic barrier products are designed to reduce airborne noises and impact sounds. These products are available in different forms, including polymeric barriers and bitumen-based barriers, and are suitable for applications in automotive, industrial, and construction sectors.
Foam Conversion Services
Foam conversion involves transforming foam materials into specific shapes and sizes to meet application needs. Acoustafoam provides services such as cutting, moulding, laminating, and fabrication to create customized foam products for various industries.
Class 0 Foam
Class 0 foam is a fire-resistant material treated with a mineral compound to prevent combustion. It is used in high-risk applications, such as engine rooms and industrial settings, for its excellent sound absorption and safety properties.
Conclusion
Foam moulding, particularly polyurethane foam moulding, is a pivotal technology in the manufacturing industry. Acoustafoam’s expertise in this field ensures the delivery of high-quality, durable, and customized foam products that meet diverse industry needs. From automotive components to acoustic barriers and foam conversion services, Acoustafoam continues to innovate and provide solutions that enhance product performance and design. For all your foam moulding needs, Acoustafoam is the partner you can rely on for excellence and reliability.
In summary, foam moulding represents a blend of technical expertise and creative design, offering a wide range of applications and benefits. Whether you require robust automotive components, effective acoustic barriers, or tailored foam solutions, Acoustafoam’s comprehensive services ensure that your needs are met with precision and quality.