Understanding the Importance and Evolution of Solder Materials in Electronics
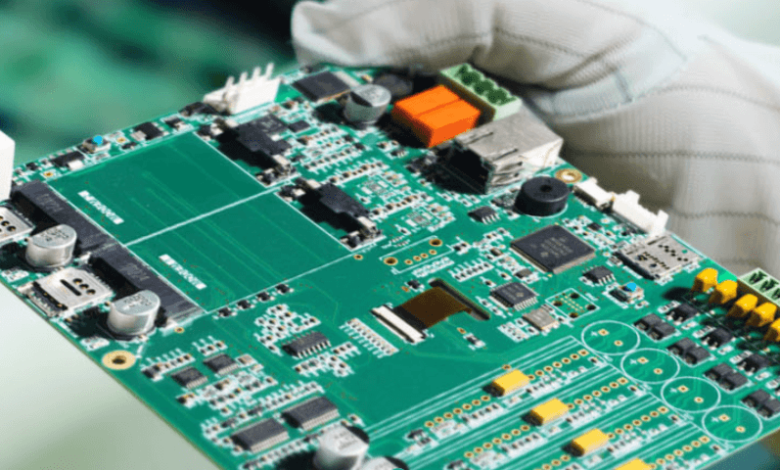
Solder materials are essential to the functionality and reliability of electronic devices. Acting as both a mechanical and electrical connection, solder is what bonds components to a printed circuit board (PCB), enabling the transmission of electrical signals. As technology advances, so does the need for solder materials that can meet increasingly demanding conditions and comply with stricter health, safety, and environmental standards. This article delves into the types of solder materials, their properties, industry applications, and the evolving technology that continues to push the boundaries of electronics manufacturing.
Types of Solder Materials
Solder materials come in various compositions, primarily divided into lead-based and lead-free categories. Additionally, specialty solders are designed to meet unique application needs.
Lead-Based Solders: Traditionally, lead-based solders, particularly the tin-lead alloy (often in a 60/40 or 63/37 ratio), have been the industry standard due to their low melting point (approximately 183°C) and excellent wetting properties. These solders provide strong, durable joints ideal for a range of applications. However, lead-based solders have been gradually phased out due to health and environmental concerns, as lead poses toxicity risks during manufacturing and disposal.
Lead-Free Solders: Lead-free solders have gained popularity, driven largely by regulations such as the Restriction of Hazardous Substances (RoHS) directive in the EU, which mandates the reduction of hazardous materials in electronics. The most common lead-free solder is SAC305, an alloy composed of 96.5% tin, 3% silver, and 0.5% copper, with a melting point around 217-220°C. Although lead-free solders have a higher melting point than lead-based solders, advancements in their composition are making them increasingly reliable and easier to work with.
Specialty Solders: In addition to standard lead-based and lead-free solders, specialty solders are developed for specific applications. High-temperature solders are often used in automotive or aerospace electronics that require stability in extreme conditions. Low-melting-point solders, frequently containing bismuth, are suited for temperature-sensitive applications, such as medical devices or certain consumer electronics. Each specialty solder composition is tailored to meet the demands of its unique environment, whether it be temperature resilience, flexibility, or enhanced durability.
See also: Motorcycle Maintenance: The Latest Tools and Techniques
Key Properties of Solder Materials
The effectiveness and durability of a solder material depend on several core properties that dictate its performance in various applications.
Melting Point: A lower melting point minimizes thermal stress on components during soldering, but it also means the solder is more susceptible to reflowing or softening in high-heat environments. Lead-free solders typically have higher melting points, which can demand more heat during assembly but offer better resilience under operational heat.
Wettability: Wettability measures how well the solder spreads and adheres to a surface. Proper wetting is crucial for forming strong, conductive joints that ensure reliable current flow. If a solder does not wet properly, it may lead to weak or cold joints, which can cause signal loss or intermittent connections.
Mechanical Strength: Mechanical strength is essential for maintaining stable connections under stress from vibration, shock, and thermal expansion. Stronger solder joints are particularly important in industries where electronics may face rough handling or extreme temperatures.
Thermal and Electrical Conductivity: Thermal conductivity helps dissipate heat from sensitive components, while electrical conductivity maintains signal integrity. Both properties are essential for the performance and lifespan of the device, especially in high-density or high-frequency circuits.
Applications of Solder Materials in Different Industries
Consumer Electronics: In consumer electronics, where mass production and cost-efficiency are priorities, lead-free solders are the standard choice. SAC305 is commonly used due to its balance between performance and cost-effectiveness. Devices like smartphones, laptops, and gaming consoles benefit from reliable lead-free solder joints that ensure durability without sacrificing environmental responsibility.
Automotive and Aerospace: Electronics in the automotive and aerospace sectors demand highly reliable solder materials that can endure extreme temperatures and mechanical stress. High-temperature solders, sometimes with indium or antimony, are used in these applications. For instance, automotive electronics are often subject to temperature fluctuations and vibrations, requiring solders that won’t degrade under such conditions.
Medical Devices: Medical electronics require a high level of reliability and minimal potential for adverse reactions in sensitive environments. Lead-free solders are preferred in most cases, and specialty solders with biocompatible properties may be used in devices that come into direct contact with the human body, such as implants or diagnostic equipment.
Industrial Equipment: Industrial electronics often require solder materials with high mechanical strength to withstand continuous usage and exposure to environmental factors like humidity, dust, and varying temperatures. Specialty solders with additional elements like nickel or gold are sometimes used to enhance corrosion resistance in harsh industrial environments.
Advances in Solder Technology
The continuous push for smaller, more powerful electronics has led to significant advancements in solder materials. Researchers and manufacturers are developing new alloys and methods to meet the demands of modern devices.
Improved Lead-Free Solders: New formulations in lead-free solders aim to reduce melting points while enhancing strength and conductivity. Alloys with small additions of rare earth elements, such as cerium or lanthanum, have shown improved mechanical and thermal performance, helping lead-free solders achieve the reliability of lead-based solders.
Nano-Enhanced Solders: Nano-enhanced solders incorporate nanoparticles, often of silver or copper, to improve the properties of lead-free solders. These nanoparticles help lower the melting temperature and improve wetting characteristics, which is particularly beneficial for high-density applications in compact electronics.
Self-Healing Solders: Self-healing solders are an emerging technology designed to repair minor cracks or voids in solder joints caused by stress or thermal cycling. These solders contain polymer-based microcapsules that release a repair agent under stress, potentially extending the lifespan of solder joints in applications prone to constant movement or vibration, such as automotive or wearable electronics.
Environmentally Friendly and Biodegradable Solders: With increasing awareness of environmental impact, the electronics industry is exploring biodegradable solders and other eco-friendly options. These solders aim to minimize waste and reduce reliance on non-renewable resources, aligning with global sustainability goals and the growing demand for eco-friendly manufacturing.
Challenges in Solder Materials
Despite significant progress, challenges remain in the adoption and development of advanced solder materials.
Higher Melting Points of Lead-Free Solders: Lead-free solders generally require higher temperatures during soldering, which can strain equipment and delicate components. Manufacturers must carefully balance temperature to avoid component damage while ensuring a robust solder joint.
Cost of Specialty Alloys: Specialty solders, especially those containing elements like silver, indium, or rare earth metals, can be costly. As such, their use is often limited to applications where specific performance properties justify the added expense.
Reliability of Lead-Free Solder in High-Stress Environments: Lead-free solders can be more brittle than lead-based solders, leading to potential reliability concerns in high-stress or high-vibration environments. Research into alloying additives continues to address these limitations, but challenges remain.
Conclusion
Solder materials are a foundational component in electronics manufacturing, bridging the mechanical and electrical connections that allow devices to operate. As technology progresses, solder materials must keep pace, evolving to meet the needs of smaller, faster, and more reliable electronic devices while complying with environmental standards.
From lead-based solders to the latest nano-enhanced, self-healing, and eco-friendly alloys, the advancements in solder materials have been essential for the development of modern electronics. Continued research and innovation in this field will be vital as the electronics industry confronts new challenges and higher expectations, ensuring that solder materials will continue to support the demands of future technologies.