Exploring Pigging System Applications: Revolutionizing Fluid Transfer Across Industries
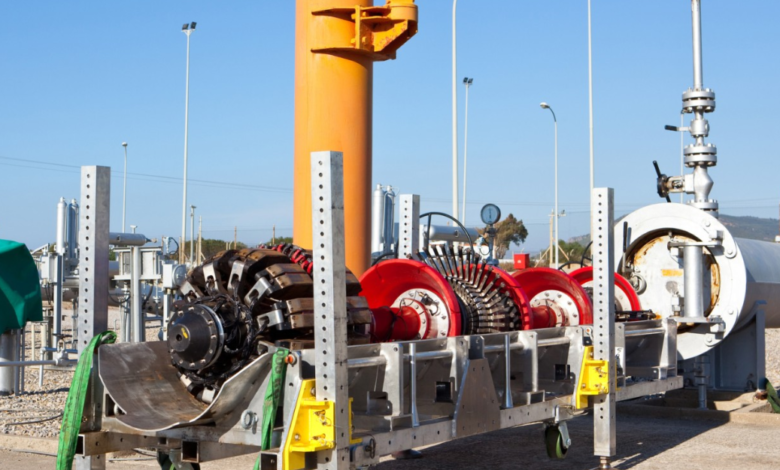
In today’s competitive industrial landscape, the demand for cleaner, faster, and more sustainable operations has grown dramatically. Whether it’s food processing, paint manufacturing, or chemical production, one technology that continues to provide outstanding value is the pigging system. Specifically, pigging system applications have expanded far beyond their original scope and are now critical to operations in a wide range of industries.
Pigging systems are used to recover product, clean pipelines, and minimize waste during changeovers and batch processing. This article explores the diverse pigging system applications, why they matter, and how they support operational efficiency, product integrity, and environmental responsibility.
What Are Pigging Systems?
Pigging systems use a specially designed device, commonly referred to as a “pig,” to clean and clear pipelines. The pig is pushed through the pipe using compressed air or gas. It is made from flexible, hygienic, and chemical-resistant materials that allow it to closely follow the interior contours of the pipeline, effectively pushing out residual product.
A modern pigging system includes:
- A pig launcher and receiver
- Pipelines with pig-detectable sensors
- Control valves
- Compressed air or nitrogen to move the pig
- Automation via PLC or SCADA systems
The purpose of pigging systems is to make operations more efficient by recovering leftover product, reducing downtime, minimizing cleaning effort, and supporting quick product changeovers.
See also: The Role of Technology in Modern Trading Platforms
The Evolution of Pigging System Applications
Originally used in the oil and gas industry to clean and inspect long-distance pipelines, pigging systems have now become commonplace in many sectors dealing with viscous, high-value, or hygienically sensitive fluids. The evolution of pigging technology has allowed it to be applied in various industries, offering not only cleaning benefits but also major economic and environmental advantages.
Common Pigging System Applications by Industry
1. Food and Beverage
One of the most widespread pigging system applications is in the food and beverage sector. This industry deals with a range of liquid and semi-liquid products such as sauces, juices, dairy, chocolate, and oils—all of which require high standards of hygiene.
Benefits in this sector include:
- Recovery of residual product for increased yield
- Prevention of cross-contamination between flavors or allergens
- Reduced water and chemical use during cleaning
- Faster changeovers for high mix, low volume production
A tomato ketchup manufacturer, for example, can save hundreds of liters of product daily using a pigging system, which would otherwise go to waste during pipeline clearing.
2. Cosmetics and Personal Care
Cosmetic products are often thick, viscous, and expensive. Formulations also vary greatly in color, scent, and active ingredients. This makes pigging extremely useful for product recovery and batch separation.
Common applications include:
- Transferring creams, gels, lotions, and shampoos
- Avoiding fragrance cross-contamination
- Reducing cleaning and downtime
- Maximizing yield for high-margin products
Pigging also helps companies meet regulatory demands for clean processing, especially in factories that handle sensitive skin-care items.
3. Paints, Coatings, and Inks
Pigging is a game-changer in the paint and coatings industry. Pigments, resins, and solvents can be hard to clean, and traditional flushing leads to significant product loss and excessive use of cleaning agents.
Key applications:
- Product recovery between color batches
- Reducing solvent-based cleaning waste
- Avoiding material mixing between incompatible products
- Supporting environmental sustainability initiatives
With paint ingredients being costly and environmentally sensitive, a pigging system helps reduce VOCs, minimize effluent, and increase profitability.
4. Pharmaceuticals
Pharmaceutical production requires strict hygiene, cleanliness, and batch integrity. Pigging systems in pharma are designed to meet high standards of quality and validation.
Applications in this industry:
- Transferring oral suspensions, syrups, or viscous APIs
- Ensuring complete product recovery from costly batches
- Reducing time and resources spent on cleaning validation
- Enhancing traceability through automated control systems
Because pharmaceutical ingredients are tightly controlled, pigging helps minimize waste while maintaining production standards.
5. Chemical Industry
In chemical manufacturing, pigging systems are used for safety, efficiency, and yield improvement. Chemicals may be hazardous, expensive, or reactive, so precise product handling is critical.
Applications include:
- Recovering product from pipeline transfers
- Enhancing operator safety by limiting chemical exposure
- Managing batch changes in shared pipelines
- Supporting sustainability by reducing cleaning waste
Pigging also prevents the mixing of incompatible materials, which could result in dangerous reactions or compromised product integrity.
Emerging Pigging System Applications
Beyond traditional sectors, pigging is now being applied in emerging fields and specialized applications such as:
- Plant-based milk and beverage lines in sustainable food processing
- Flavor and fragrance production where cross-contamination ruins product quality
- CBD oil and herbal extract production where high recovery is essential
- Water treatment and cleaning chemical distribution networks
These new pigging system applications demonstrate the adaptability of the technology to evolving market needs and regulatory requirements.
Benefits of Pigging Systems Beyond Cleaning
While cleaning is a major function, pigging systems offer far-reaching benefits:
✅ Product Recovery
Pigging can recover up to 99.5% of the product left in pipelines, improving profitability and reducing waste.
✅ Reduced Downtime
Faster product changeovers mean less idle time for machines and greater production throughput.
✅ Lower Cleaning Costs
With minimal product left in the lines, less water and fewer chemicals are needed for cleaning, saving on materials and disposal.
✅ Better Sustainability
Pigging helps achieve corporate sustainability goals by minimizing waste, water usage, and environmental impact.
✅ Improved Safety
By limiting human exposure to chemicals or hot cleaning fluids, pigging supports a safer work environment.
Choosing the Right Pigging System
Selecting the right pigging system depends on the specific application. Considerations include:
- Type and viscosity of product
- Frequency of product changeovers
- Required hygiene standards
- Pipe layout and size
- Automation and control needs
Custom-designed systems offer better performance and ROI compared to one-size-fits-all solutions.
Real-World Case Example
A U.S.-based cosmetics company implemented a pigging system on its shampoo production line. Before installation, it lost nearly 5 gallons of product per changeover and spent 30 minutes flushing lines.
Post-installation:
- Product loss dropped by 95%
- Cleaning time cut by half
- ROI achieved within 9 months
This real-world example proves that pigging system applications are not just technically effective but also economically justifiable.
Final Thoughts
As industries seek smarter ways to reduce waste, improve efficiency, and meet regulatory demands, pigging system applications have proven to be an innovative and impactful solution. Whether you’re producing yogurt, ink, adhesives, or hair conditioner, there’s a pigging system tailored to your needs.
With proper implementation, pigging technology enhances sustainability, boosts profitability, and simplifies production—making it a strategic choice for companies worldwide.